Help With Labor Operations
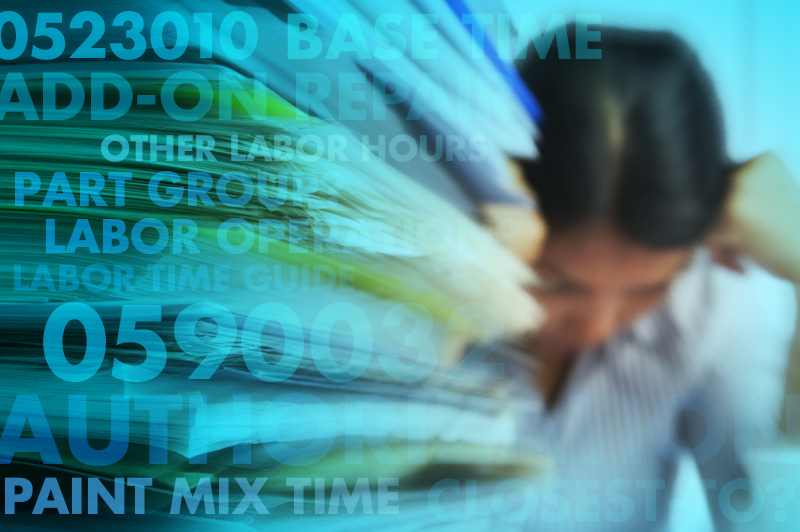
Applying Labor Operations In A Perfect World
A warranty repair is made, the technician types or writes what was done to be recorded on the job card, a labor operation is applied that fits the repair, a claim is submitted to GM, and the dealer gets paid. Sounds pretty simple, doesn’t it?
In a perfect world, warranty job cards have clear and concise customer concerns, cause of failures, and corrections written in a systematic, legible way. The part name charged out on the job card is the same name the technician uses and it’s the same description in the Labor Time Guide (LTG). The next step is to open up the LTG and find a labor operation. But as we all know, the world isn’t perfect. The role of warranty administrator can be complicated at best, and downright impossible if the technician’s documentation isn’t fully explained and your resources aren’t resourceful enough. Labor operation coding is a process that requires written, detailed information so that a labor operation can be matched to reimburse the dealer for warranty repairs made. It is also the way GM learns of product failures. It’s an important assignment.
Finding The Right Labor Operation
Completed warranty repairs must have a labor operation assigned. These labor operations are found in GM’s LTG, which is a series of labor operations contained in repair groups. The more you know about how an automobile operates, the easier it will be for you to find a labor operation since you will have a better idea in which repair group to look into. If you are not so mechanically inclined, there are other ways to find a labor operation. A labor operation can be found by performing a word search. But, the technician’s descriptions and/or the part name written on the job card must be the same word as found in the Labor Time Guide. For example, the technician states that the alternator was replaced. The LTG refers to this component as a generator. Sometimes a module is called a control. A pump is also called a module. Word searches generally work best for an experienced warranty administrator who is familiar with which word to input. Word searches are a helpful tool; the more you work at it, the better you will get.
Some labor operations aren’t in the LTG. If a repair made is from information found in a specific bulletin, there may be a labor operation assigned that is exclusive to following the procedures contained within that bulletin. These labor operations aren’t published in the LTG and the warranty administrator will only know they exist when the technician includes the bulletin number in their comments. Every job card that references a bulletin number should be confirmed in Service Information and checked for an applicable labor operation. Recall, Service Update, and Special Coverage labor operations are also not in the LTG.
EPIC is also a resource for finding more descriptive wording for a component. The part information field in EPIC provides an accurate description by entering the part number and clicking on the part name that is populated.
“Closest To” Labor Operations
There are instances when a “closest to” labor operation must be found and used on a claim. Many labor operations are for the replacement of a component only. If the technician repaired a component as opposed to replacing it, the replace labor operation may be the closest labor operation and more than likely the appropriate one to use. Repairing a component may involve more time and OLH. If the technician has a separate time recording, a detailed repair description, and service management signature or initials, date, time, and approval reasoning, up to 2.0 hours OLH can be claimed. There are times when repairing takes less time than replacing. The labor time should be reduced to reflect the recorded time the technician has involved with the repair.
A “closest to” labor operation is used when you are unable to find a labor operation to match the repair performed. Discuss the repair with the technician, explaining that you are unable to find a labor operation that fits the repair performed. The technician may be able to add more details to their correction documentation that will aid in finding a labor operation. Also helpful is seeing where the component replaced is located on the vehicle and what other components may be near or attached to the failed one. Between seeing the component on the vehicle and getting technician input, look for a labor operation that is in the ballpark and submit the claim. If you receive a reject that states the labor operation is not compatible to the vehicle, or the part is incompatible to the labor operation and your research has hit a dead-end, H-route the claim to GM with a clear explanation. Sometimes, there just isn’t a labor operation.
Add-on Repair Labor Operations
Get the GM Added Operation Warranty Stamp to help remember to authorize the job card for an added operation repair.
A labor operation is necessary for each repair made and there should be only one repair made for each customer concern. Repairs that are added to the job card after the initial write-up are considered an add-on repair. All added repairs require service management involvement and authorization prior to work being performed. Add-on repairs must be signed, dated, the time indicated, and a full explanation written by the service manager. If additional repairs are required because what failed on the vehicle caused damage to other parts of the vehicle, report only the labor operation of the failed component. Collateral or consequential damage labor time is submitted as OLH to the failed labor operation and extra parts get added to the part count. These claims must often be H-routed for excessive parts or when OLH exceeds the dealer’s 2.0 hour empowerment. Conversely, if additional repairs are necessary to satisfy the customer’s single concern and the additional repair is a separate failure, a second labor operation is submitted. This second repair is considered an add-on repair and may overlap or be related to the first labor operation submitted and require service management authorization.
Authorization Code R
Repeat repairs-comebacks are defined as the same or potentially similar repairs on the same VIN, but not on the same day or same job card. These repairs must authorized by service management prior to work being performed with authorization code R. Repeat repairs-pyramiding is defined as the same or potentially similar repair or overlapping repairs on the same VIN, on the same job card. These repairs must be authorized by service management prior to transaction submission with authorization code R. In both scenarios, authorization must be in the form of an explanation, date, time and signature/initials.
Who Applies The Labor Operations
In most dealerships, a warranty administrator applies the labor operation to the warranty claim. In some dealerships, the warranty process is a shared responsibility involving service management, service advisors, parts management, and office personnel. While smaller dealerships may not be able to justify a full time warranty administrator, it’s important to note that too many hands involved in warranty administration can result in missed revenue, increased rejected claims, differences of opinions, and a lack of ownership. It’s clearly stated that technicians are not allowed to assign labor operations, including labor time, and service management is responsible for ensuring that the proper labor operations and times are being applied and warranty expense is being monitored. Outsourcing warranty may be a good option for those dealerships that don’t have a dedicated warranty administrator with the knowledge and experience of the warranty process.
It takes a team effort to properly apply labor operations to warranty job cards. There must be a solid customer concern, cause of failure, and correction story that can be clearly understood by anyone reading the job card. Without this information, it is much more difficult to find the proper labor operation for the repair performed. Eventually, just like a lot of tasks, we get better and better the more we work at the task on hand. Before you know it, you’ll be a warranty pro!

The Warranty Administration Program is a subscription-based, educational program developed by jlwarranty and offered through GM Dealer Equipment. The program educates service personnel to properly claim, collect, and keep all expenses related to the warranty repair, according to GM Service Policies & Procedures. Stay up-to-date on pressing warranty topics, interact with other warranty professionals, enjoy complete access to the online video training library, and have all the tools and support you need for warranty administration success. Benefits include a monthly newsletter, quick reference publications, online forums, video training, and more.
Learn More